(1)生産管理システム導入の成功と失敗
品質、納期、在庫、コストの問題を解決するためには『ものづくり』の改善と同時に
ものづくりがスムーズに流れるように、前提として良い計画、良い調達、良い対策
(計画と実績の対比によりタイムリーに対策:通常遅れる)が必要です。
これを支援するのが生産管理システムです。
しかし、ほとんどの製造業の生産管理システムは成果の面から評価すると、満足のいく
ものではありません。
経営者、管理者から見た場合、評価の対象は納期、在庫、コストの面から見て成果が上がったか。
生産管理担当者から見た場合の評価は従来の生産管理業務の煩雑さから逃れられたかに重点がおかれます。
導入した生産管理システムが稼働しないだけが失敗ではありません。
成果が上がらない場合も失敗の範疇に入ります。
レ
@システムが稼働しない ----- |
× |
Aシステムは稼働したが運用が大変、かつ、運用効果も出ない |
× |
Bシステムが稼働し運用は従来より楽になった。しかし運用効果は出ていない |
△ |
Cシステム運用をしている部分(一部のみ)は効果があるが、全体に拡大しない |
△ |
Dシステムは稼働したが運用が大変、しかし、運用効果は出ている |
○ |
Eシステムが稼働し、他の改善とともに運用効果が大きくなり始めている |
◎ |
欧米では新しい概念は3文字で表現することが多いようです。
表は製造業に関するシステムに関係する3文字熟語がメディアに登場した時期を示しています。
それぞれ概念そのものは、それぞれの条件において正しいのですが、自社の条件が整わない(適合しないor改善できない)場合は、
形だけの導入になり成果があがりません。
(2)信頼の失墜
生産管理システムを何とかしたいと考えている経営者は多いのですが、過去の失敗あるいは成果が上がらないことから、
生産管理システムを信用していない経営者が多いのも事実です。
その結果、生産管理解決のための決断が遅れ再構築が遅れています。
この世界同時不況の状況で、受注の確保、増加は必須課題ですが、品質、納期、コスト
の問題を解決しないと、目標は達成できません。どうしたらよいでしょうか?
(3)自社の受注/生産形態などの分類
見込み生産方式か受注生産方式かの分類だけでは不十分です。受注生産といっても継続見込受注生産、断続受注生産、
個別受注生産、一品受注生産があります。
見込み生産は製品まで見込み生産する場合とユニットまで見込み生産(一般には受注生産に分類)があります。
自社の生産が加工型か組立型あるいは装置型(機械装置型、プロセス装置型)の分類も
重要です。生産ラインの形態としてジョブショップ型、フローショップ型、自動ライン型、一個流し型と分類することもあります。
すべて、工場を見ると単独ではなくこれらの組み合わせです。
(5)開発かパッケージ利用か
自社の生産管理システム再構築は自社の受注/生産の特性に合わせて、開発(社内・外部)するか、パッケージを利用するか、
基本パッケージをカストマイズして自社用にするかに大別されます。いずれも長所短所があります。
(6)自社に適した生産管理方式の選択
以上検討した内容と下図の内容を明確にすると自社に適合した生産管理方式は絞られます。
以上、自社の受注形態、生産形態に適合した生産管理方式は絞られます。
(4)生産管理方式の選択
生産管理方式を大別すると、発注点管理、製番管理、MRP、かんばん、スケジューラー、APSがあり、企業は単独あるいは、
これらの組み合わせで運用しています。
図はそれぞれ日本で運用された時期を表しています。製番管理は戦前は号機管理などと呼ばれて運用されていたのでこれを含めると
開始時期は図より早くなります。
(7)適合しないパッケージを選択した場合
生産管理システムを導入あるいは再構築する場合、関係する部門を上げると、ソフト開発メーカー、
システムを販売するSI(システムインテグレータ)、生産管理システムを導入するプロジェクト、
システムを直接あるいは間接的に運用する部門(ユーザー)、成果を期待する経営者・幹部です。
自社に適合しないパッケージ(種類、機能)を選んだ場合は、システムが稼働しないか、一部の製品や工程の運用にとどまります。
また、無理に全面運用しても効果を上げることは難しいかもしれません。また、適合しないからと言って、各部門のクレームを
吸い上げてカストマイズをしすぎると費用が膨大になります。また後のメンテナンスが大変です。
パッケージを導入する場合、一番重要なのは自社に適合するかどうかですが、これがわかるSIやコンサルタントに巡り合うのは中々大変です。
既に導入するパッケージを決めていた場合、詳細な要件定義やフィットギャップ分析(自社の業務に適合するか否か)で
適合しない部分が多くあることがわかっても、後の祭りです。適合させるためにカストマイズしても、カストマイズ地獄に陥る危険性があります。
運用が始まる前(導入過程)にカストマイズする場合と、運用が始まってからシステム運用者側から使いにくいというクレームに
対応するためにカストマイズする場合、ユーザ部門が必要とする機能が無いことが分かったために追加する場合があります。
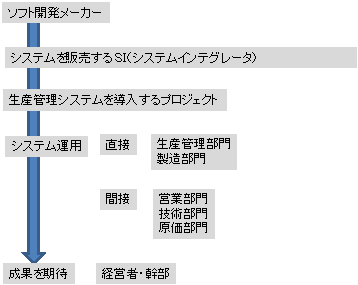
(初期の導入スケジュール通りに稼働しないあるいは導入開始後成果が上がらない場合、
経営者・幹部からのクレームがあります。
クレームが重なると、本来、従来、実施してきた業務を少しパッケージに合わせて変えるだけで済む内容も、
全て、従来やってきた内容はできるようにしなさい(カストマイズ)ということになります。
(8)SIとコンサルタント
SIの営業さんの仕事はまず、自社が扱っているパッケージをいかに多く販売するかが使命です。
コンサルタントはSIと連携しているコンサルタントと全く独立しているコンサルタントがいます。
前者のコンサルタントは、パッケージ導入が決まってから、上流工程の要件定義、フィットギャップ分析の結果、
お客様の業務をパッケージ合わせて変更してもらう(かってBPRビジネスプロセスエンジニアリングと称した)
ための指導の役目を持ちます。
この種のコンサルタントの場合、この会社には経験からパッケージは合わないと判断しても、
パッケージ導入はやめた方がいいとは、言えないことがほとんどです。
後者は、SIとは独立したコンサルタントなので、ユーザサイドでパッケージの選定をします。
しかし、このコンサルタントがシステム部門出身なのか、実際に多くの生産現場、生産管理の実務を経験した先生なのかによって、
適合度の判断が変化します。
かって、中堅製造業の生産管理システムがオフコン全盛の場合はリスクを考えて、比較的高い価格設定ができました。
現在、パソコンによる生産管理では利幅が少なく、クレームでカストマイズが発生すると即,
赤字(正味かかる追加費用をもらえない場合が多い)になります。
そこで、SIさんの防衛としては、システム価格をリスクを加味して高めの設定します。
あるいは、導入するシステムの機能の範囲を契約書で明確に明示します。
また、システムから伝票出力され、実績を入力開始したところで最終検収とします。
前者の価格を高めに設定した場合は、競争見積もりでは、ほとんどの受注できないことが多いのですが。
後者の場合、一応、SIさんのリスクは避けることはできますが、残された問題が解決されない場合、
動かないシステム、あるいはシステムは稼働しても成果が出ないシステムになる危険性が高くなります。
(9)成果を上げる
納期、在庫、コスト、品質の問題点を解決するためには生産管理システムが稼働しただけでは難しいです。
生産管理システムは納期、在庫、コストの問題点解決を支援するインフラの一部です。
品質は直接生産管理システムとは関係ないように考えますが、品質の安定向上には適正な生産管理システムは必要不可欠です。
生産管理システムは成果を上げるために必要不可欠のものですが、製造業で満足のいく生産管理システムが
運用されている企業は数少ないでしょう。
最初に改善マップに掲げた総合的な改善があって初めて成果を上げることができます。
現場改善、調達改善、設計部門の改善、営業部門の改善を同時進行させなければ成果は上がらないのです。
そのようなことは分かっている。しかし、中堅、中小企業の場合、人材不足でそこまで手が回らない。
というのが経営者の悩みです。しかし、この問題点を解決する方法はあります。
生産管理システムは導入すると最低10年間は使います。
過去に2度失敗していると失われた20年になります。3度失敗していると30年です。
金融危機に端を発した世界同時不況の中で、生産管理システムの失敗は許されません。
最低、納期 と品質は守らないと少なくなった受注すら確保することが難しくなります。
最低、納期と品質を守るためのシステム改善は必要になります。
納期と在庫はリンクしているので在庫の改善も必然的に必要です。

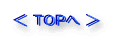

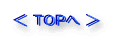